بوابة العالم العربي لهواة الرو بوت
بوابة العالم العربي لهواة الرو بوت
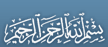


اذا كنت احد المهتمين في مجال علوم الروبوت والذكاء الاصطناعي ولديك تجربة في هذا المجال واحببت التعريف بنفسك للاخرين والتعرف على خبرات الاخرين في مجال الروبوت والذكاء الاصطناعي او مشاركة معلوماتك مع ذوي الاهتمام ، يمكنك الان نشر تجربتك ومعلومات عن اجازاتك واهتمامتك في هذا المجال من خلال موقع الجمعية العربية للروبوت

رد: بوابة العالم العربي لهواة الرو بوت
اذا كان لديك نشاط مميز في مجال الروبوت ، لا تترد وبضع موضوعك هنا
رد: بوابة العالم العربي لهواة الرو بوت
Robot configurations.
Typical workspace for common robot configurations

Typical workspace for common robot configurations

رد: بوابة العالم العربي لهواة الرو بوت
Robotics is the branch of technology that deals with the design, construction, operation, and application of robots


رد: بوابة العالم العربي لهواة الرو بوت
Arachnophobes look away now, because the Hexapod spider robot is coming to get you!


رد: بوابة العالم العربي لهواة الرو بوت
The Aldebaran Robotics Nao H25 Humanoid Robot Academic Edition is a programmable, 57-cm tall humanoid robot. It has NAOqi, the embedded NAO software, includes a fast, secure reliable and cross-platform, distributed robotics framework that provides a solid foundation on which developers can leverage and improve NAO's functionality. A 6-watt-hour battery that provides NAO with 1.5 or more hours of autonomy, depending on usage.
• Body with 25 degrees of freedom (DOF) whose key elements are electric motors and actuators
• Intel ATOM 1,6ghz CPU (located in the head) that runs a Linux kernel and supports Aldebaran's proprietary middleware (NAOqi)
• Second CPU (located in the torso

• Body with 25 degrees of freedom (DOF) whose key elements are electric motors and actuators
• Intel ATOM 1,6ghz CPU (located in the head) that runs a Linux kernel and supports Aldebaran's proprietary middleware (NAOqi)
• Second CPU (located in the torso

رد: بوابة العالم العربي لهواة الرو بوت
Remote controlled’ material handling equipment
Posted by CJ Samson on July 28, 2010 in Mechanical Engineering Projects, Mechanical Seminar Topics, Robots / 128 Comments
Prior to the introduction of the so called “Material handling equipment” humans had to perform physical labor to carry out heavy duty tasks. This could be made possible by employing a huge number of workers. However, when the goods came in bulk unloading and loading turned out to be a very time consuming affair. The use of Material handling equipment in logistics has played a significant role in making the loading and unloading activities easier and faster.
Ask yourself the question “Why are ‘Remote controlled’ material handling equipment used?” and almost instantly you arrive at the logical answer that the chief benefit would be allowing personal to control their machine from a safe distance.
Remote control can be achieved by two different modes:
1) Radio frequency (RF) Signals
RF signals are further divided into two categories.
a) Narrow-band system b) Spread spectrum system.
2) Infrared light
Infrared method works by transmitting a beam of light
Infrared mode of radio control is preferred over RF signals because of the safety and precision that it offers. Since the infrared method works by transmitting a beam of light, once the beam is out of sight, the beam is obstructed and the controls turn off. That is, the operator must always be in view of the RCMHE, which in turns aids safety as the full visibility of the operator over the machine is critical. Precise, in the sense that with the use of RF technology there is always a chance of interference with other signals and might lead to accidents, Infrared remote control makes this type of mistake impossible.
Applications:
1) Transfer of components from one container to another especially fragile objects
2) Transfer of hazardous/explosive objects
3) Operation in high temperature environment

Posted by CJ Samson on July 28, 2010 in Mechanical Engineering Projects, Mechanical Seminar Topics, Robots / 128 Comments
Prior to the introduction of the so called “Material handling equipment” humans had to perform physical labor to carry out heavy duty tasks. This could be made possible by employing a huge number of workers. However, when the goods came in bulk unloading and loading turned out to be a very time consuming affair. The use of Material handling equipment in logistics has played a significant role in making the loading and unloading activities easier and faster.
Ask yourself the question “Why are ‘Remote controlled’ material handling equipment used?” and almost instantly you arrive at the logical answer that the chief benefit would be allowing personal to control their machine from a safe distance.
Remote control can be achieved by two different modes:
1) Radio frequency (RF) Signals
RF signals are further divided into two categories.
a) Narrow-band system b) Spread spectrum system.
2) Infrared light
Infrared method works by transmitting a beam of light
Infrared mode of radio control is preferred over RF signals because of the safety and precision that it offers. Since the infrared method works by transmitting a beam of light, once the beam is out of sight, the beam is obstructed and the controls turn off. That is, the operator must always be in view of the RCMHE, which in turns aids safety as the full visibility of the operator over the machine is critical. Precise, in the sense that with the use of RF technology there is always a chance of interference with other signals and might lead to accidents, Infrared remote control makes this type of mistake impossible.
Applications:
1) Transfer of components from one container to another especially fragile objects
2) Transfer of hazardous/explosive objects
3) Operation in high temperature environment

رد: بوابة العالم العربي لهواة الرو بوت
Underwater Robot With A Sense Of Touch
The robot dives into the sea, swims to the submerged cable and carries out the necessary repairs, but the person controlling the robot does not have an easy task. It is pitch dark and the robot’s lamp does not help much. What’s more, the current keeps pulling the robot away from where it needs to carry out the work.
In future, the robot could find its own way. A sensor will endow it with a sense of touch and help it to detect its undersea environment autonomously.
One component in this tactile capability is a strain gauge. If the robot encounters an obstacle, the strain gauge is distorted and the electrical resistance changes. The special feature of our strain gauge is that it is not glued but printed on – which means sensor can be applied to curved surfaces of the robot.
The single printed strip is just a few ten micrometers wide, i.e. about half the width of a human hair. As a result, the strain gauges can be applied close to each other and the robot can identify precisely where it is touching an obstacle. The sensor is protected from the salt water by encapsulation.
To produce the strain gauges, the research scientists atomize a solution with nanoparticles to create an aerosol. A software system guides the aerosol stream to the right position. Focusing gas shrouds the beam and ensures that it does not fan out.

The robot dives into the sea, swims to the submerged cable and carries out the necessary repairs, but the person controlling the robot does not have an easy task. It is pitch dark and the robot’s lamp does not help much. What’s more, the current keeps pulling the robot away from where it needs to carry out the work.
In future, the robot could find its own way. A sensor will endow it with a sense of touch and help it to detect its undersea environment autonomously.
One component in this tactile capability is a strain gauge. If the robot encounters an obstacle, the strain gauge is distorted and the electrical resistance changes. The special feature of our strain gauge is that it is not glued but printed on – which means sensor can be applied to curved surfaces of the robot.
The single printed strip is just a few ten micrometers wide, i.e. about half the width of a human hair. As a result, the strain gauges can be applied close to each other and the robot can identify precisely where it is touching an obstacle. The sensor is protected from the salt water by encapsulation.
To produce the strain gauges, the research scientists atomize a solution with nanoparticles to create an aerosol. A software system guides the aerosol stream to the right position. Focusing gas shrouds the beam and ensures that it does not fan out.

رد: بوابة العالم العربي لهواة الرو بوت
A distinguishing feature of robotics is its multidisciplinary nature — to successfully design robotic systems one must have a grasp of electrical, mechanical, industrial, and computer engineering, as well as economics and business practices. The purpose of this chapter is to provide a background in all these areas so that design for robotic applications may be confronted from a position of insight and confidence. The material covered here falls into two broad areas: function and analysis of the single robot, and design and analysis of robot-based systems and workcells.


رد: بوابة العالم العربي لهواة الرو بوت
Designing a Simple Navigating Robot
This robot called NIRo , and it requires several key hardware components to effectively navigate an environment and avoid obstacles:
Embedded controller – for sensor data acquisition, decision making, and motor control
Infrared sensors – for detecting objects within a certain distance on both sides and rear of the robot platform
Ultrasonic sensors – for detecting objects in front of the robot because they cover a larger area
H-bridges – for directing the current from the battery to the motors in the correct direction to move the motors forward or backward
The Figure shows where each hardware component is located on NIRo. Table 1 provides a detailed parts list.

This robot called NIRo , and it requires several key hardware components to effectively navigate an environment and avoid obstacles:
Embedded controller – for sensor data acquisition, decision making, and motor control
Infrared sensors – for detecting objects within a certain distance on both sides and rear of the robot platform
Ultrasonic sensors – for detecting objects in front of the robot because they cover a larger area
H-bridges – for directing the current from the battery to the motors in the correct direction to move the motors forward or backward
The Figure shows where each hardware component is located on NIRo. Table 1 provides a detailed parts list.


» بوابة العالم العربي لهواة الرو بوت
» ☼◄بوابة العالم العربي لاخبار شركات السيارات" متجددة "►☼
» مكتبة صور العالم العربي لاحلى الشاحنات في العالم
» التصحر في العالم العربي
» الدردشة على العالم العربي
» ☼◄بوابة العالم العربي لاخبار شركات السيارات" متجددة "►☼
» مكتبة صور العالم العربي لاحلى الشاحنات في العالم
» التصحر في العالم العربي
» الدردشة على العالم العربي
صفحة 1 من اصل 1
صلاحيات هذا المنتدى:
لاتستطيع الرد على المواضيع في هذا المنتدى